FanCheng Сочетание двух методов производства роботов делает Университет Тунцзи связующим звеном между
Опубликован в:2020-07-13
The hybrid bridge is formed by winding fine carbon fibers around a 3D printed metal frame. It is made by college students in Shanghai using two emerging robot manufacturing technologies. Students attending the Digital Futures international 2019 Summer Seminar at Tongji University collaborated with the local research studio Fab union to design a bridge that can accommodate more than 20 people.
The hybrid bridge made by robot is an exploration of two relatively new construction methods - Large Metal 3D printing (such as metal 3D printing for the worlds first bridge in mx3d) and filament winding (as shown by elytra in the beetle wing style of the University of Stuttgart).
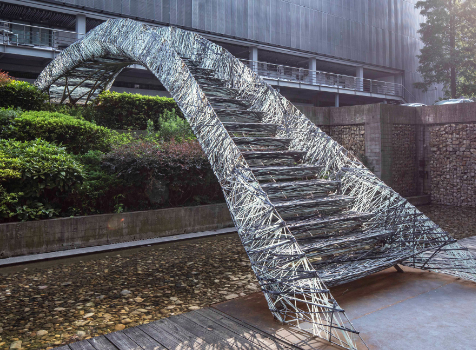
Compared with traditional building methods (such as subtractive manufacturing or casting), both technologies can save money, materials and energy, and students want to see how they work together.
Their hybrid approach does not involve templates or molds, and they believe it provides a lot of design freedom.
They used 3D printing to construct the skeleton steel foundation of the bridge and wound carbon and glass fibers to produce mesh stairs and handrails.
They used topology optimization software to strip all unnecessary materials from the design. Finally, the 11.4m long bridge needed 263kg of steel. At the thinnest point, the thickness of the steel frame is 20 cm.
The construction phase takes 20 days and requires a total of four robots - two for each manufacturing method.
The structure was pre assembled off-site, then installed on the waterscape facilities of the school of architecture and urban planning of Tongji University, and stayed there from July 2019 to October 2019.
"Robot manufacturing is a high-precision manufacturing technology that combines advanced structural analysis and optimization methods," said Philip F. yuan, an architect who led the team and a scholar at Tongji University
He added: "the project proves that intelligent buildings have great material and energy-saving potential in the construction field."
The team deliberately removed all decorative elements from the design to focus entirely on its substance.
"The project presents a clean, accurate and robust structure," they said "The light from the sun passes through the glass fiber to produce a soft and soothing light."
Their multi-material robot manufacturing team is one of 12 teams in the Digital Futures 2019 series. Others focus on topics such as enhanced wood assembly, smart city decision-making, AI in urban design, generative design and overall construction or holographic auxiliary architecture.
The hybrid bridge made by robot is an exploration of two relatively new construction methods - Large Metal 3D printing (such as metal 3D printing for the worlds first bridge in mx3d) and filament winding (as shown by elytra in the beetle wing style of the University of Stuttgart).
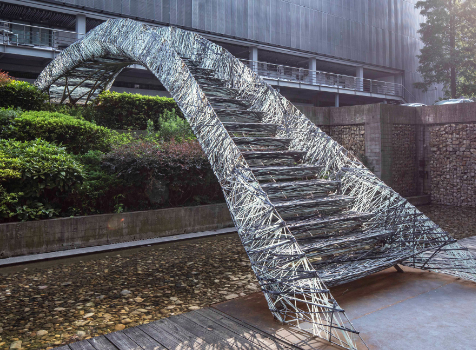
Compared with traditional building methods (such as subtractive manufacturing or casting), both technologies can save money, materials and energy, and students want to see how they work together.
Their hybrid approach does not involve templates or molds, and they believe it provides a lot of design freedom.
They used 3D printing to construct the skeleton steel foundation of the bridge and wound carbon and glass fibers to produce mesh stairs and handrails.
They used topology optimization software to strip all unnecessary materials from the design. Finally, the 11.4m long bridge needed 263kg of steel. At the thinnest point, the thickness of the steel frame is 20 cm.
The construction phase takes 20 days and requires a total of four robots - two for each manufacturing method.
The structure was pre assembled off-site, then installed on the waterscape facilities of the school of architecture and urban planning of Tongji University, and stayed there from July 2019 to October 2019.
"Robot manufacturing is a high-precision manufacturing technology that combines advanced structural analysis and optimization methods," said Philip F. yuan, an architect who led the team and a scholar at Tongji University
He added: "the project proves that intelligent buildings have great material and energy-saving potential in the construction field."
The team deliberately removed all decorative elements from the design to focus entirely on its substance.
"The project presents a clean, accurate and robust structure," they said "The light from the sun passes through the glass fiber to produce a soft and soothing light."
Their multi-material robot manufacturing team is one of 12 teams in the Digital Futures 2019 series. Others focus on topics such as enhanced wood assembly, smart city decision-making, AI in urban design, generative design and overall construction or holographic auxiliary architecture.