Фан Ченг из Массачусетского технологического института разработал роботизированные захваты, которые могут работать с гибкими объектами.
Опубликован в:2020-07-15
These thin and small things, such as ropes, wires or cables, are also relatively fragile for humans. For robots, it is even more difficult to control. Manipulator picking up is challenging, and most robot grippers cant handle them at all. MIT researchers have now created a robotic gripper that can more closely mimic the way humans handle such flexible objects.
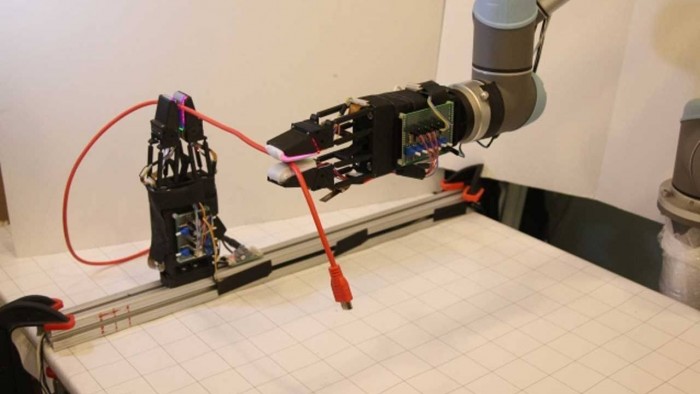
The system uses a pair of soft robot grippers with high-resolution tactile sensors to manipulate the freely moving cable. The team created a two finger gripper, which is light and fast, and can adjust its strength and position in real time. At the top of each gripper is a vision based (gelsight) sensor, which is made of soft rubber and embedded with a camera.
The gripper is installed on the mechanical arm, which can move as part of the control system. Gelsight sensor is used to estimate the position of the cable between fingers and measure the friction force of cable sliding. The system has two controllers running in parallel. One controller can adjust the grip force and the other controller can adjust the grip position to keep the cable firmly grasped.
The gripper can reliably track the USB cable from the random grasping position, and combined with the second gripper, it can move the cable like a person and find the end of the cable. The gripper can also adapt to cables of different materials and thicknesses. The robot can complete the routine actions of human beings when inserting earplugs into mobile phones. The robot starts from the free floating earplug cable. When it feels that the plug contacts the finger, it can slide the cable, stop with both fingers, adjust the plug and insert the plug into the jack.
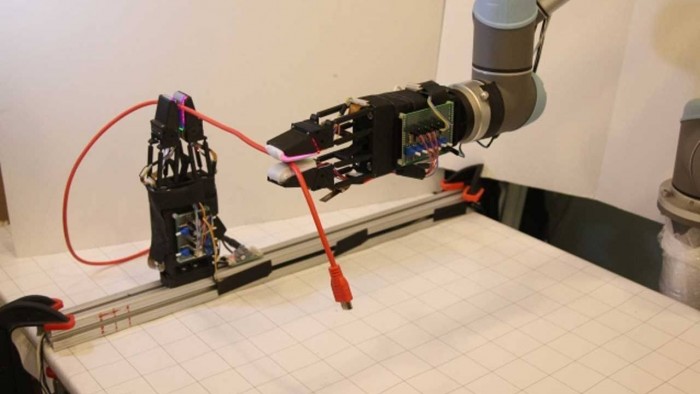
The system uses a pair of soft robot grippers with high-resolution tactile sensors to manipulate the freely moving cable. The team created a two finger gripper, which is light and fast, and can adjust its strength and position in real time. At the top of each gripper is a vision based (gelsight) sensor, which is made of soft rubber and embedded with a camera.
The gripper is installed on the mechanical arm, which can move as part of the control system. Gelsight sensor is used to estimate the position of the cable between fingers and measure the friction force of cable sliding. The system has two controllers running in parallel. One controller can adjust the grip force and the other controller can adjust the grip position to keep the cable firmly grasped.
The gripper can reliably track the USB cable from the random grasping position, and combined with the second gripper, it can move the cable like a person and find the end of the cable. The gripper can also adapt to cables of different materials and thicknesses. The robot can complete the routine actions of human beings when inserting earplugs into mobile phones. The robot starts from the free floating earplug cable. When it feels that the plug contacts the finger, it can slide the cable, stop with both fingers, adjust the plug and insert the plug into the jack.